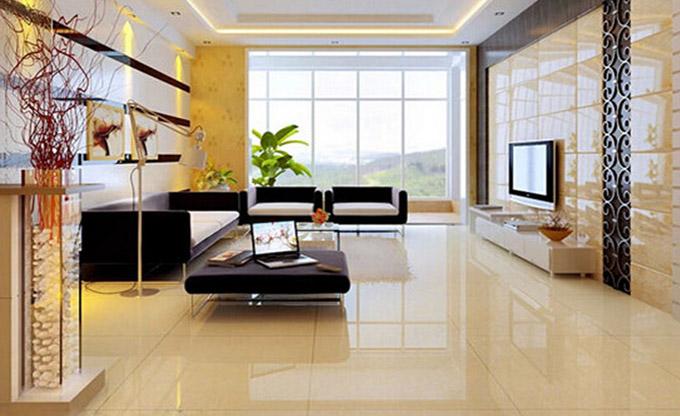
课题 | Q235钢角接TIG焊 | ||||||||
班级 | 18机械 | 授课地点 | 氩弧焊实训室 | 课时 | 4 | 授课人 | 惠亚虎 | ||
授课 内容 | 1.介绍学习本课程的重要意义 2.对学生提出一些要求 3.简单提出重、难点内容 4.回顾学生上节课操作时的要点 5.学习新课 | ||||||||
课型 | 新授 | 教学媒体 | 氩弧焊焊机及辅助设备 | ||||||
教学目标 | 1. 了解Q235钢角接氩弧焊的应用领域 2. 学会Q235钢角接氩弧焊工艺参数的选择原则 3. 掌握Q235钢角接氩弧焊的操作技能 | ||||||||
重点难点 | 1. 本课程学习的重要性 2.氩弧焊的操作技术 | ||||||||
学生情况 分 析 | 学生对氩弧焊都已经进行过为期一周的实训,对于氩弧焊的应用及重要性都能很好的接受。 | ||||||||
教法选择 | 讲解+练习+分析+练习 | ||||||||
任务四 Q235钢角接TIG焊
学习目标
1.了解Q235钢角接氩弧焊的应用领域。
2.学会Q235钢角接氩弧焊工艺参数的选择原则。
3.掌握Q235钢角接氩弧焊的操作技能。
任务提出
生产中,箱型结构,支架、脚座等板T型接头最为常见,如图所示
3
141
4
150
图1-4-1Q235钢角接TIG焊
任务分析
实际上任何焊接方法的平角焊操作都有一定难度,特别是较大焊角尺寸时,根部不易焊透,立板咬边,平板焊角偏大,表面成形难以控制。钨极氩弧焊明弧焊接,给操作带来方便,熔池易于观察和控制,但操作不当也会造成根部未焊透缺陷。高温停留时间适中,否则产生晶间腐蚀,降低接头性能。应选择合适焊接电流,焊接速度,横向摆动幅度。
相关知识
钨极氩弧焊常见缺陷及防止措施
1、气孔的产生原因及防止措施
(1)产生气孔的原因
1)工件、焊丝表面有油污、氧化皮、铁锈。
2)在潮湿的空气中焊接。
3)氩气的纯度较低,含杂质较多。
4)氩气保护不良以及熔池高温氧化等。
(2)防止产生气孔的措施
1)工件及焊丝应清洁并干燥。
2)氩气纯度应符合要求。
3)熔池应缓慢冷却。
4)遇风时,加挡风板施焊。
2、裂纹产生原因及防止措施
(1)产生裂纹的原因
1)焊丝选择不当。
2)焊接顺序不正确。
3)焊接时高温停留时间过长。
4)母材含杂质较多,淬硬倾向大。
(2)防止产生裂纹的措施
1)选择合适的焊丝和焊接参数,减小晶粒长大的倾向。
2)选择合理的焊接顺序,使工件自由伸缩,尽量减小焊接应力。
3)采用正确的收弧方法,填满弧坑,减少弧坑裂纹。
4)对易产生冷裂纹的材料,可采用焊前预热、焊后缓冷的措施。
3、夹杂及夹钨的产生原因及防止措施
(1)产生夹杂及夹钨的原因
1)工件和焊丝表面不清洁或焊丝熔化端严重氧化,当氧化物进入熔池时便产生夹杂。
2)当钨极与工件或焊丝短路,或电流过大使钨极端头熔化落入熔池中,则产生夹钨。
3)接触引弧时容易引起夹钨。
(2)防止产生夹杂及夹钨的措施
1)焊前对工件、焊丝进行仔细清理,清除表面氧化膜。
2)加强氩气保护,焊丝端头应始终处于氩气保护范围内。
3)采用高频振荡或高压脉冲引弧。
4)选择合适的钨极直径和焊接参数。
5)正确修磨钨极端部尖角。
6)减小钨极伸出长度。
4、咬边产生原因及防止措施
(1)咬边产生原因
1)电流过大。
2)焊枪角度不正确。
3)焊丝送进太慢或送进位置不正确。
4)当焊接速度过慢或过快时,熔池金属不能填满坡口两侧边缘。
5)钨极修磨角度不当,造成电弧偏移。
(2)防止产生咬边的措施
1)正确掌握熔池温度。
2)熔池应饱满。
3)焊接速度要适当。
4)正确选择焊接参数。
5)正确选用钨极的修磨角度。
6)合理填加焊丝。
5、未熔合与为焊透产生的原因及防止措施
(1)产生未熔合及未焊透原因
1)焊接电流过小,焊接速度太快。
2)对接间隙小,坡口钝边厚,坡口角度小。
3)电弧过长,焊枪偏向一边。
4)焊前清理不彻底,尤其是铝合金的氧化膜未清除掉。
(2)防止未熔合及未焊透的措施
1)正确选择焊接参合素。
2)选择适当的对接间隙和坡口尺寸。
3)正确掌握熔池温度和调整焊枪、焊丝的角度,操作时焊枪移动要平稳、均匀。
任务实施
一.焊前准备
1.劳保 穿好棉质或皮质工作服,绝缘鞋,戴好工作帽,绝缘手套,卫生口罩,平光镜,头戴式遮光面罩等。
2.母材 Q235钢板150×50×4,检查钢平直度,并修整。钨极氩弧焊对铁锈油污非常敏感,氩气没有脱氧和去氢的能力,当坡口周围存在污物时,极易产生气孔等缺陷。为保证焊接质量,用角磨机打磨坡口两侧正反面25㎜内,除锈、除油,去污,露出金属光泽。
3.焊机 选用WSM-300或WSM-400直流钨极氩弧焊机,直流正接
电源。选择操作方式(4步),调整上下坡时间。检查设备气路、电路是否接通。钨极端部形状是否合适,清理喷嘴内壁飞溅物,使其干净、光滑,以免保护气通过受阻。
检查设备状态,电缆线接头是否接触良好,焊钳电缆是否松动,避免因接触不良造成电阻增大而发热,烧毁焊接设备。检查安全接地线是否断开,避免因设备漏电造成人身安全隐患。
4.辅助工具 备好钢锯条,扁铲、手锤、角磨砂轮,钢丝刷、钢板尺,焊缝尺等。
5.焊材 焊丝 根据母材型号,选择H08Cr19Ni10Ti焊丝,直径ф2.0㎜焊丝。
钨极 选用直径ф2.4㎜铈钨极,修磨钨极端部成30°圆锥角,为使电弧更集中,不留小平台,尽量使磨削纹路与母线平行,延长钨极使用时间。如图1-3-3所示。
ф2.5㎜
30°
图1-3-3 钨极端部修磨形状
保护气体 选择纯度99.99%的氩气作保护气,检查并调整气体流量。
6.确定焊接工艺参数
表1-8 不锈钢角接TIG焊焊接工艺参数
层次 | 钨极直径㎜ | 喷嘴直径 ㎜ | 伸出长度 ㎜ | 氩气流量 L/min | 焊丝直径 ㎜ | 焊接电流 A |
定位焊 | 2.4 | 10~14 | 5~6 | 8~10 | 2 | 60~80 |
打底层 | 2.4 | 10~14 | 5~6 | 8~10 | 2. | 60~80 |
二、装配与焊接定位
1. 装配与定位焊
I形坡口角接,装配间隙=0,否则热量散失,根部容易造成未焊透。试件两端点固,反变形约3°左右。压紧试件,钨极伸出长度5~6㎜,喷嘴接触平立两版,钨极对准试件左侧根部,按动引弧电钮引燃电弧,对根部加热,带根部熔化形成熔池,填加焊丝,向右移动电弧。焊点长度10~15㎜,然后调整间隙(击打试件右侧,使立板与平板紧密接触),再点固右侧。图1-4-2所示。
45°
70~80°
45°
2.焊接
焊角高度3毫米,不需多层焊,在点固焊点的背面采用单层单道焊。为获得较较好的焊缝成形,采用左向摇摆焊法。调节焊接电流,收弧电流,戴好头盔面罩,左手握焊丝,右手握焊枪,距右端15~20㎜处喷嘴接触试件平立两板,按动引弧按钮引燃电弧,电流开始上升,调整喷嘴高度,电弧长度约2 ~3㎜,调整焊丝角度为10~15°,缓慢回拉电弧到右端端部稍作停顿,此时,钨极对准根部尖端,工作角45°角,前进70~80°角;待根部熔化并形成熔池,填加一滴焊丝,向前摇摆电弧,待形成新熔池,再填加一滴焊丝。如图1-4-3。根据焊角高度的需要,调整焊丝送给量,使焊角高度达到3㎜为好。焊道余高不易太大。
45°
70~80°
45°
10~15°
焊枪前进角度
焊枪工作角度
图1-4-3Q235钢T型接头焊枪角度及摇摆运弧方法
焊接过程中,也可以两板为支点交替摆动喷嘴,向前移动电弧,但尽量不要使钨极摆动太大,减小电弧横向摆动幅度。
理想的焊缝颜色应该是银白色或金黄色,如果焊缝颜色为黑色或深蓝色,为不合格焊缝。所以在焊接中在保证熔合良好的情况下,尽量加快焊接速度,以降低熔池高温停留时间。 焊缝截面外形以平、凹为合格。图1-4-4所示。
三、焊缝外观检测
1.自检
①试件焊接完成后,用敲渣锤、锉刀等清理熔渣、飞溅,用钢丝刷清理焊缝。
②检查试件焊后角变形,是否平整,一般不大于3°。
③检查焊缝是否有裂纹,表面气孔,夹渣,咬边等缺陷。
④检查焊缝整体直线度,焊缝宽度是否宽窄一致。
⑤检查焊缝整体余高是否高低一致。
⑥检查焊缝是否有接头不良,超高或脱节现象。
⑦检查焊缝背面是否有未焊透,未熔合,凹坑或焊瘤。
⑧根据评分标准进行扣分。
2.互检和专检
按照自检的条款逐项进行检查,并按评分标准扣分,之后与自检得分对照,找出不同之处,在老师的指导下修改之。
任务评价
表1-9 T型接头T接头水平角焊缝评分标准
姓名 | 学号 | 合计分 | ||||||||||||
检查项目 | 标准、分数 | 焊 缝 等 级 | 实际得分 | |||||||||||
Ⅰ | Ⅱ | Ⅲ | Ⅳ | |||||||||||
焊脚尺寸 | 标准(mm) | 3 | ﹥3,≤3.5 | ﹥3.5,≤4 或 ﹥2.5,≤3 | <2.5,﹥4 | |||||||||
分数 | 10 | 8 | 6 | 0 | ||||||||||
焊缝凸度 | 标准(mm) | ≤0.5 | ﹥0.5,≤1 | ﹥1,≤1.5 | ﹥1.5 | |||||||||
分数 | 10 | 8 | 6 | 0 | ||||||||||
垂直度 | 标准(mm) | ≤1 | ≤2 | ≤3 | ﹥3 | |||||||||
分数 | 5 | 3 | 2 | 0 | ||||||||||
表面气孔 | 标准:(个) | 无 | 有 | 有 | 有 | |||||||||
分数 | 5 | 0 | 0 | 0 | ||||||||||
焊道层数 | 标准:(道) | 1 | ||||||||||||
分数 | 5 | 0 | ||||||||||||
咬边 | 标准(mm) | 0 | 深度≤0.5 且长度≤15 | 深度≤0.5 长度﹥15, ≤30 | 深度﹥0.5 或长度﹥30 | |||||||||
分数 | 15 | 10 | 5 | 0 | ||||||||||
折断试验 | 根部熔深 | 标准(mm) | ≥1 | ≥0.5 | ≥0 | <0 | ||||||||
分数 | 20 | 15 | 10 | 0 | ||||||||||
条状缺陷 | 标准(mm) | 0 | ≤2 | ≤3 | ﹥3 | |||||||||
分数 | 15 | 10 | 6 | 0 | ||||||||||
点状缺陷 | 标准(个) | 0 | ≤Φ1 数目:3个 | ≤Φ1 数目:5个 | >Φ1或 数目>5个 | |||||||||
分数 | 15 | 10 | 6 | 0 | ||||||||||
思考与练习
1. 钨极氩弧焊有哪些特点?钨极氩弧焊设备有哪几类?
2. 钨极氩弧焊焊接工艺参数对焊缝质量有什么影响?
3. 钨极氩弧焊I形坡口角焊的操作技能有哪些要点?
钨极氩弧焊可用于几乎所有金属和合金的焊接,但由于其成本较高,主要用于不锈钢、高合金钢、高强钢以及铝、镁、铜、钛等有色金属及其合金的焊接。由于其电弧密度高,热量集中,内应力小,焊缝的塑性韧性好,不易产生过热组织、未焊透、气孔、夹渣、裂纹等缺陷,因此钨极氩弧焊广泛应用于航空航天、化工、锅炉压力容器、医疗器械及炊具等工业部门。
更多推荐
焊接,焊缝,焊丝,熔池,电弧,产生,检查,是否
发布评论